คุณภาพบริการสุขภาพกับระบบลีน (Quality Services with Lean System)
โดยรองศาสตราจารย์ ดร.พาณี สีตกะลิน
คุณภาพ (Quality)
คือ สิ่งที่บ่งบอกถึงประสิทธิภาพ ความพึงพอใจ มาตรฐานที่ได้รับบริการสุขภาพ เป็นกระบวนการที่เกี่ยวข้องกับผู้มีส่วนได้ส่วนเสีย (Stake holder) โดยคำนึงถึงคุณภาพเป็นสำคัญ คุณภาพของบริการสุขภาพนี้คือ ความปลอดภัยในชีวิตของผู้รับบริการ นอกจากนี้แล้วจะต้องตอบสนองความต้องการของผู้รับบริการ ผู้มีส่วนได้ส่วนเสียทุกภาคส่วนบนพื้นฐานมาตรฐานของวิชาชีพและมาตรฐานของสถานบริการสุขภาพ ปัจจุบันสถานบริการสุขภาพมีการปรับตัว ในคุณภาพบริการอยู่ตลอดเวลา ประกอบกับผู้บริโภค/ผู้มีส่วนได้ส่วนเสียมีการรับ-ส่งข้อมูลข่าวสารด้านบริการสุขภาพแบบ ไร้พรมแดนมากขึ้น ดังนั้นสถานบริการสุขภาพและผู้บริหารจึงจำเป็นต้องพัฒนาคุณภาพบริการให้เกิดความยั่งยืนตอบสนองต่อการเปลี่ยนแปลงทางสังคมอย่างรวดเร็ว
ในการจัดบริการสุขภาพที่มีคุณภาพนั้น มีเครื่องมือที่หลากหลายนำไปสู่คุณภาพบริการ ในที่นี้ขอนำเสนอระบบลีนหรือการผลิตแบบลีน (Lean Manufacturing) ซึ่งแพร่หลายในวงการอุตสาหกรรม โดยสามารถนำมาประยุกต์ใช้กับระบบบริการสุขภาพได้
ความหมายของลีน
คำว่า “ลีน” หมายถึง ความผอมบาง ถ้าเปรียบเทียบและมองในแง่บวก หมายถึง องค์การที่มีขนาดกระชับ มีความสามารถในการปรับตัว สามารถตอบสนองความต้องการของลูกค้าและสังคมได้ทันท่วงที โดยมีการดำเนินการที่ปราศจากความสูญเสียในทุกๆ กระบวนการ และมีประสิทธิภาพเหนือคู่แข่ง
วิวัฒนาการระบบลีน
ก่อนที่จะรู้จักกับระบบลีน ควรทำความรู้จักประวัติและความเป็นมาของระบบลีน ระบบนี้ มีจุดเริ่มต้นในวงการอุตสาหกรรมผลิตรถยนต์ในศตวรรษที่ 19 ต่อ 20 ก่อนที่จะพัฒนาเป็นระบบลีนในอุตสาหกรรมรถยนต์นั้น การผลิตรถยนต์สมัยต้นศตวรรษที่ 20 ใช้ฝีมือและแรงงานมากไม่มีระบบ ที่เรียกว่าสายการผลิต บริษัทผลิตรถยนต์ส่วนใหญ่ต้องอาศัยทักษะและความชำนาญของพนักงาน เป็นหลัก ดังนั้นต้นทุนการผลิตต่อหน่วยจะสูง แต่ผู้ผลิตก็สามารถผลิตรถยนต์ได้หลากหลายตามความต้องการของลูกค้า ต่อมาในช่วงต้นศตวรรษที่ 20 นายเฮนรี่ ฟอร์ด ผู้ก่อตั้งบริษัทฟอร์ด มอเตอร์ ได้ริเริ่มแนวคิดในการสร้างสายการผลิตให้มีการไหลเวียนคล้ายลักษณะของการไหลสายน้ำ และใช้แนวคิดที่ว่าอุปสรรคที่อยู่ในกระบวนการผลิตคือ ความสูญเปล่าและไม่เกิดคุณภาพ โดยใช้ระบบสายพานลำเลียงซึ่งเป็นนวัตกรรมในการผลิตรถยนต์ที่มีคุณภาพในสายการประกอบรถยนต์ (Moving Assembly line) ของบริษัทฟอร์ด มอเตอร์ และใช้ชิ้นส่วนมาตรฐานที่สามารถเปลี่ยนทดแทนกันได้ ทำให้ใช้เวลาในการผลิตลดลง และส่งต่อไปยังกระบวนการผลิตขั้นต่อไป การผลิตลักษณะเช่นนี้เป็นลักษณะเหมือนการผลิตสินค้าสำเร็จรูปจำนวนมากๆ จึงเรียกการผลิตระบบนี้ว่าเน้นปริมาณ คือเน้นการผลิตจำนวนมากเพื่อลดต้นทุนต่อหน่วยผลิตให้ต่ำลงโดยเฉพาะต้นทุนทางอ้อม ระบบการผลิตลักษณะนี้ประสบความสำเร็จมากและเป็นที่กล่าวขวัญในประเทศสหรัฐอเมริกาในยุคนั้น ซึ่งผลิตรถยนต์ฟอร์ดโมเดลที่เป็นรุ่นยอดนิยมและจำหน่ายดีมากถึงแม้ว่าจะมีเพียงสีดำสีเดียว ตลาดขณะนั้นยังเป็นของผู้ผลิตเพราะมีผู้ผลิตน้อยราย การผลิตยังมีจำนวนน้อยแต่ความต้องการมาก demand over supplied เท่ากับว่าผลิตจำนวนเท่าใด ก็ขายได้หมด
ยุคเข้าสู่ระบบลีนจากประเทศสหรัฐอเมริกาสู่ประเทศญี่ปุ่น
ต่อมานายอิจิ โทโยดะ และนายโทอิจิ โอโนะ ผู้บริหารบริษัทโตโยต้า ได้นำแนวคิดของ เฮนรี่ ฟอร์ด มาพัฒนาต่อยอดในการปรับปรุงระบบการผลิตของบริษัทโตโยต้าที่ประเทศญี่ปุ่น แต่บริบทของบริษัท ไม่เหมาะกับระบบนี้เนื่องจากปัจจัยหลายประการคือ ในช่วงเวลานั้นประเทศญี่ปุ่นอยู่ในภาวะแพ้สงคราม สถาวะเศรษฐกิจและปัจจัยอื่นๆ จึงไม่เหมาะกับระบบนี้ นายซิฮิโอ ซินโง ที่ปรึกษาบริษัทโตโยต้า ได้กล่าวว่าแนวคิดการผลิตแบบโตโยต้า เป็นระบบที่พัฒนาอย่างต่อเนื่องให้เหมาะสมกับบริบทของตลาดและประเทศ โดยมุ่งเน้นการผลิตจำนวนมาก ด้วยขนาดรุ่นการผลิตที่เล็กและระดับสินค้าคงคลังต่ำ ซึ่งเป็น การนำแนวคิดแบบลีนของนายเฮนรี่ ฟอร์ด มาประยุกต์ให้เกิดระบบการผลิตแบบโตโยต้าที่เรียก “การปฎิบัติที่เป็นเลิศ” (Best Practice) ของระบบการผลิตลีน
การเริ่มต้นของคำว่า ระบบลีนและแนวคิดของระบบลีน
ในปี ค.ศ.1990 นายเจมส์ ออแม็ค และนายแดเนียล โจนส์ ได้เขียนเปรียบเทียบปัจจัยแห่งความสำเร็จระหว่างอุตสาหกรรมรถยนต์ในประเทศต่างๆ คือ ญี่ปุ่น ยุโรป สหรัฐอเมริกา โดยเปรียบเทียบการเพิ่มขีดความสามารถในการจัดการกระบวนการ และเริ่มใช้คำว่า “ระบบการผลิตแบบลีน” ตั้งแต่นั้นมา
วิวัฒนาการของระบบการผลิตแบบลีน เริ่มต้นจากระบบการผลิตงานฝีมือมาสู่การผลิตระบบ เน้นเชิงปริมาณแล้วพัฒนามาสู่ระบบการผลิตแบบลีนที่มีความยืดหยุ่นในการผลิตที่ให้ผลผลิตสูง ลดต้นทุนหรือต้นทุนต่ำ เพื่อรองรับสภาพปัจจุบันของวงการผลิตที่ต้องการลดขั้นตอนวงจรการผลิต ให้สั้นลง
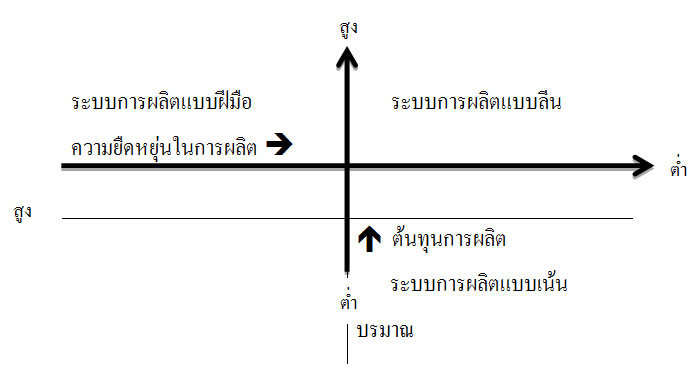
ภาพที่1 แสดงการเปรียบเทียบระหว่างระบบการผลิตแบบฝีมือ ระบบเน้นปริมาณและระบบการผลิตแบบลีน
แนวคิดระบบลีน (Concept of Lean)
แนวคิดระบบลีน คือ วิธีการที่มีระบบแบบแผนในกระบวนการ ระบุและกำจัดความสูญเสีย สิ่งที่ไม่เพิ่มคุณค่า/มูลค่าในกระบวนการ โดยใช้การดำเนินตามจังหวะความต้องการของลูกค้าด้วย ระบบดึง (pull) ทำให้เกิดสภาพการไหลของงานอย่างต่อเนื่อง ไม่มีอุปสรรค และมีการปรับปรุงอย่างต่อเนื่องเพื่อสร้างคุณค่าให้ระบบอยู่เสมอ ประกอบด้วย 5 ขั้นตอน คือ
ขั้นตอนที่ 1 ระบบสร้างคุณค่าของผลิตภัณฑ์/บริการ ในมุมมองของลูกค้าภายในและลูกค้าภายนอก โดยผู้บริหารทุกระดับจะต้องให้ผู้ร่วมงานมีส่วนร่วมในการสร้างคุณค่า การให้บริการในมุมมองของผู้มีส่วนได้ส่วนเสียทุกภาคส่วน นั่นคือลูกค้าภายในและภายนอก
ขั้นตอนที่ 2 การสร้างกระแสคุณค่าในทุกๆ ขั้นตอนของการดำเนินงานตั้งแต่จุดเริ่มต้น คือ การวางแผน จนถึงจุดสิ้นสุดของการดำเนินการในกระบวนการและพิจารณาร่วมกันระหว่างผู้ที่มีส่วนได้ส่วนเสียว่า กิจกรรมใดที่ไม่เพิ่มคุณค่าและเป็นความสูญเสีย เพื่อลดกิจกรรมดังกล่าวในกระบวนการและให้เกิดความตระหนักในความสูญเสีย และหาวิธีการลดความสูญเสียที่เกิดขึ้น
ขั้นตอนที่ 3 พิจารณาทำให้กิจกรรมในกระบวนการดำเนินงานมีคุณค่าเกิดการดำเนินงานได้อย่างต่อเนื่อง (flow) โดยไม่มีปัญหาอุปสรรคหรือข้อขัดข้องต่างๆ ที่ทำให้เกิดความสูญเสียในกระบวนการ สามารถดำเนินงานได้อย่างไหลลื่น
ขั้นตอนที่ 4 ใช้ระบดึง (pull) ผู้บริหารให้ความสำคัญเฉพาะสิ่งที่ลูกค้าต้องการเท่านั้น ไม่ว่าจะเป็นลูกค้าภายในหรือลูกค้าภายนอกก็ตาม โดยต้องใช้เครื่องมือวิเคราะห์ว่าจะดึงสิ่งที่ลูกค้าต้องการ โดยให้ความสำคัญเป็นอันดับแรกและสำคัญที่สุดเท่านั้น
ขั้นตอนที่ 5 สร้างคุณค่าและกำจัดความสูญเปล่าที่อาจซ่อนเร้นอยู่ในส่วนเกินต่างๆ โดยกำจัดความสูญเปล่าและสร้างคุณค่าอย่างต่อเนื่อง
จากขั้นตอนทั้ง 5 ประการดังกล่าวจะเห็นได้ว่าการพัฒนาอย่างต่อเนื่องในการสร้างคุณค่าโดย ใช้แนวคิดพื้นฐานโดยใช้วงจรคุณภาพ PDCA ดังภาพ
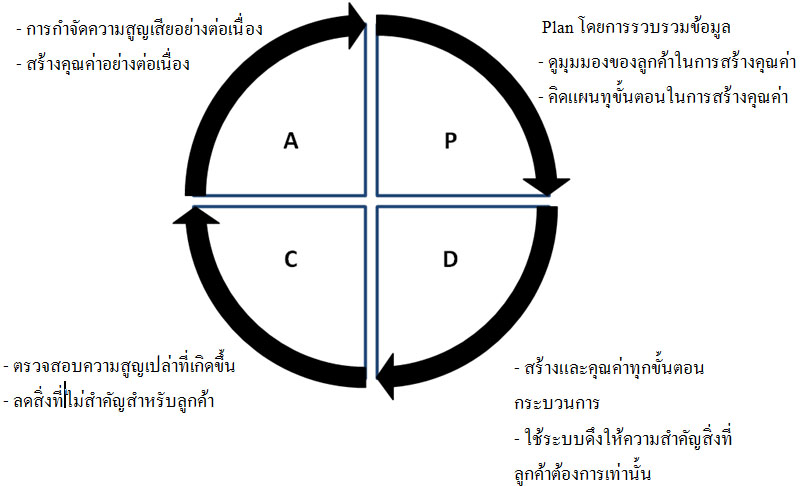
ภาพที่2 วงจรคุณภาพ
ในการสร้างระบบลีนนั้น สิ่งแรกที่ต้องจำไว้เสมอคือ จะต้องเริ่มต้นจากคนหรือพนักงาน ทั่วทั้งองค์กร โดยเฉพาะพนักงานในระดับปฎิบัติการและหัวหน้างาน โดยต้องเสริมสร้างความเข้าใจ ทำให้พนักงานมีทัศนคติที่ถูกต้อง พยายามหลีกเลี่ยงการเริ่มต้นด้วยการนำเอาเครื่องมือต่างๆ ของระบบ ลีนไปใช้ภายในองค์กร จากนั้นนจึงเริ่มวิเคราะห์สภาพปัจจุบัน วางแผนงานอย่างเป็นระบบ กำหนดเป้าหมายในการปรับปรุง แล้วจึงใช้เครื่องมือต่างๆ มาช่วยปรับปรุงอย่างต่อเนื่อง ทั้งนี้ขั้นตอนการสร้างระบบลีนแบ่งออกเป็น 7 ระยะ ดังนี้
การเตรียมความพร้อมด้านต่างๆ ได้แก่ สถานที่ เครื่องมืออุปกรณ์ที่จำเป็นบุคลากรและช่องทางการสื่อสารภายในระหว่างสมาชิกผู้ดำเนินโครงการ รวมถึงการฝึกอบรมให้ความรู้ของระบบลีนแก่ผู้บริหารและคณะทำงาน
การระบุคุณค่าของสินค้าและบริการที่ลูกค้าต้องการทั้งภายนอกและภายใน แล้วสรุป เป็นข้อกำหนด ส่วนประกอบ กระบวนการ และรายละเอียดการปฎิบัติงานโดยใช้เทคนิคการถ่ายทอดความต้องการของลูกค้าสู่ผลิตภัณฑ์ (Quality Function Deployment : QFD)
การสำรวจสถานะปัจจุบันของกระบวนการทั้งหมด แล้วสรุปบนแผนภาพกระแสคุณค่า (Value Stream Mapping) เพื่อระบุปัญหา และนำไปใช้ในการวางแผนพัฒนากระแสคุณค่าในขั้นตอนถัดไป
การประเมินสภาพของกระบวนการ ตัวชี้วัดผล และเป้าหมายของโครงการตามแนวทางของระบบลีน (LEAN Assessment) เพื่อนำไปใช้ประกอบการวางแผนพัฒนากระบวนการ
การวางแผนและดำเนินการปรับปรุงกระบวนการตามแผนภาพกระแสคุณค่าอนาคต (Future Value Stream Mapping) ร่วมกับการใช้เครื่องมือพัฒนาที่เหมาะสม (ตามโครงสร้างของระบบข้างต้น) โดยพิจารณากิจกรรมที่ไม่เพิ่มคุณค่าและเป็นความสูญเปล่าในทุกขั้นตอนจากภาพกระแสคุณค่า (Value Stream Mapping) ที่สร้างขึ้น
การขับเคลื่อนกิจกรรมตามกระแสคุณค่า (Value Stream) อย่างต่อเนื่อง เน้นเฉพาะสิ่งที่ลูกค้าต้องการ โดยการควบคุมระบบการผลิตแบบลีน ร่วมกับการสร้างระบบคัมบัง (Kunban) ซึ่งเป็นเครื่องมือสำคัญของระบบดึงการสร้างคุณค่าและกำจัดความสูญเปล่าอย่างต่อเนื่อง ด้วยการค้นหาความสูญเปล่าที่ มองไม่เห็น แล้วปรับปรุงกระบวนการด้วยระบบการผลิตแบบลีน พร้อมทั้งขยายผลสู่บริเวณอื่นๆ ไปจนถึง Supply Chain อันได้แก่ ลูกค้า ผู้ส่งมอบ และผู้รับเหมาช่วงการผลิต
------------------------------------
เอกสารอ้างอิง
http://www.pte-cal.kmutt.ac.th สืบค้นเมื่อ 6 พฤษภาคม 2556
http://eep.cpportal.net/Knowledge Sharing สืบค้นเมื่อ 7 พฤษภาคม 2556
|